Koła zębate stożkowe: sekret efektywnego przenoszenia mocy
- Budowa przekładni stożkowych: najważniejsze elementy i materiały
- Rodzaje kół zębatych stożkowych. Porównanie różnych typów konstrukcji
- Zasada działania kół zębatych stożkowych. Czemu zawdzięczają efektywność przenoszenia mocy?
- Parametry techniczne kół zębatych stożkowych. Na co zwrócić uwagę przy wyborze?
- Gdzie najczęściej używa się kół zębatych stożkowych? Zastosowania przemysłowe
Koła zębate stożkowe i wykorzystujące je przekładnie stożkowe są stosowane w wielu układach przeniesienia napędu. Ich specyficzna budowa i związane z nią właściwości umożliwiają ich w różnych gałęziach przemysłu. W tym nowym artykule wyjaśniamy, jak zbudowane są i jak działają przekładnie stożkowe oraz podpowiadamy, które parametry techniczne kół zębatych stożkowych mają największe znaczenie.
Budowa przekładni stożkowych: najważniejsze elementy i materiały
Przekładnie stożkowe składają się z dwóch kół zębatych, których zarysy tworzą powierzchnię stożków. Służą do przenoszenia momentu obrotowego między osiami ustawionymi względem siebie pod kątem prostym lub innym – w zależności od specyfiki danej aplikacji.
Standardowa przekładnia stożkowa składa się z następujących elementów:
- koło czynne (zębnik): przekazuje napęd z wału czynnego (napędowego) do drugiego koła, a następnie – wału napędzanego;
- koło bierne: odbierające napęd z pierwszego koła i przekazujące je do dalszych elementów układu;
- wały: ustawione pod kątem i osadzone na łożyskach.
Do produkcji kół zębatych stożkowych najczęściej stosuje się stal, żeliwo, aluminium, mosiądz, miedź oraz tworzywa sztuczne.
Rodzaje kół zębatych stożkowych. Porównanie różnych typów konstrukcji
W ofercie producentów tworzących części do maszyn przemysłowych dostępne są różne typy kół zębatych stożkowych. Poszczególne rodzaje różnią się między sobą konstrukcją oraz kształtem zębów i, co za tym idzie, sposobem działania. W grupującym koła zębate katalogu znajdziemy przede wszystkim:
- koło zębate stożkowe o zębach prostych: charakteryzują się zębami ułożonymi wzdłuż prostych linii, co jest najprostszym rodzajem konstrukcji. Są stosunkowo tanie w produkcji, ale mogą generować większy hałas podczas pracy;
- koło zębate stożkowe o zębach spiralnych (łukowych): zęby są ułożone wzdłuż łuków, co pozwala na bardziej płynne przekazywanie napędu i mniejsze tarcie. Dzięki temu są ciche i bardziej efektywne, ale ich produkcja jest bardziej skomplikowana, co wpływa na cenę;
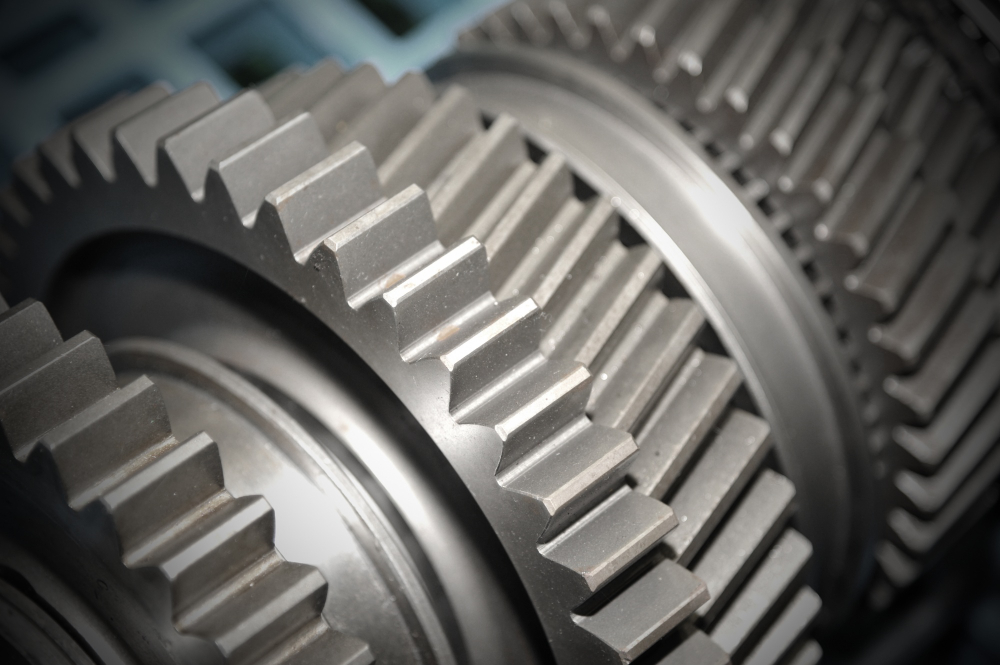
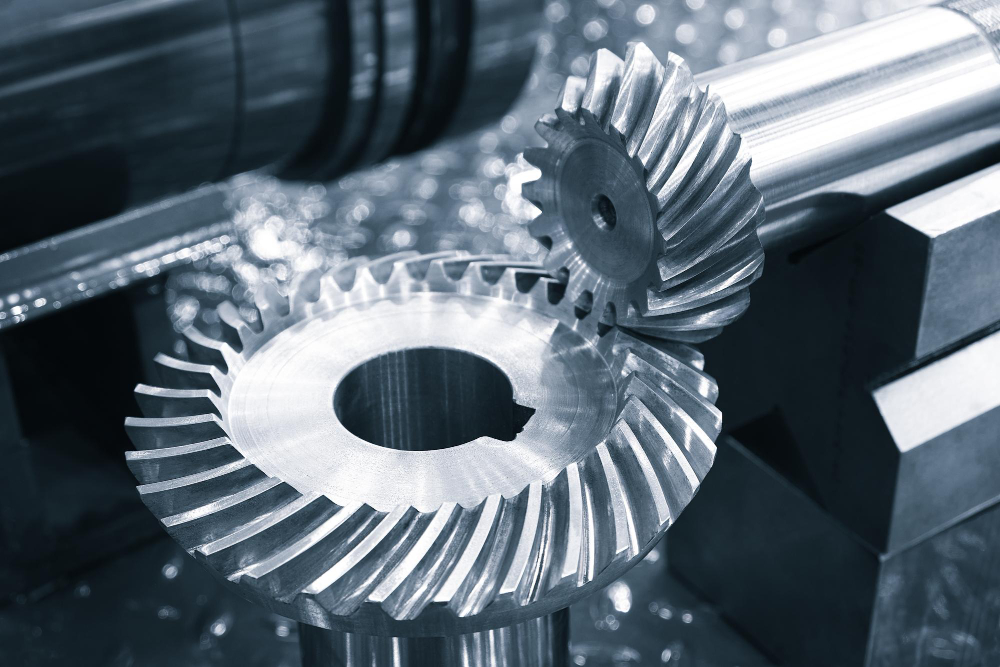
Zasada działania kół zębatych stożkowych. Czemu zawdzięczają efektywność przenoszenia mocy?
Koła zębate stożkowe przenoszą moment obrotowy poprzez zazębiające się pod kątem zęby. Efektywność przenoszenia mocy jest uzależniona od kilku czynników, wśród których największe znaczenie mają:
- kąt styku zębów: powinien umożliwiać efektywne przenoszenie momentu obrotowego przy minimalnym tarciu;
- powierzchnia kontaktu: dzięki kształtowi zębów, koła stożkowe zapewniają dużą powierzchnię stylu, co umożliwia szerokie rozłożenie obciążenia;
- precyzja wykonania.
Parametry techniczne kół zębatych stożkowych. Na co zwrócić uwagę przy wyborze?
Przeglądając katalog kół zębatych, znajdziemy ich różne warianty. By mieć pewność, że przekładnia będzie pracować sprawnie i bezawaryjnie, przy wyborze tych części maszyn, należy zwrócić uwagę kilka parametrów technicznych:
- przełożenie: określa stosunek prędkości obrotowej między kołem napędzającym a kołem napędzanym. Powinno być dopasowane do specyfiki aplikacji – obciążeń, oczekiwanej prędkości i innych czynników;
- materiał: ze względu na dużą wytrzymałość i możliwość pracy pod dużymi obciążeniami, najczęściej spotykane są koła stalowe. Mosiądz, miedź i tworzywa sztuczne używane są przede wszystkim tam, gdzie oczekuje się odporności na korozję. Ten ostatni materiał na koła zębate nie wymaga ponadto smarowania;
- kąt i profil zębów: wpływa na efektywność przenoszenia napędu oraz poziom hałasu generowanego podczas pracy.
Gdzie najczęściej używa się kół zębatych stożkowych? Zastosowania przemysłowe
Koła zębate stożkowe znajdują zastosowanie tam, gdzie konieczne jest przeniesienie napędu pod kątem. Do ich najważniejszych zastosowań należy zaliczyć:
- przemysł motoryzacyjny: w przekładniach różnicowych w samochodach oraz we wkrętarkach i narzędziach elektrycznych na liniach montażowych;
- przemysł maszynowy: w obrabiarkach przekładnie stożkowe umożliwiają precyzyjne ustawienie i przenoszenie napędu.
Koła zębate stożkowe to ważny element wielu mechanizmów. Ich najważniejsze zalety to możliwość przeniesienia napędu pod kątem, efektywność i trwałość. Różnorodność ich typów umożliwia wykonanie przekładni idealnie dostosowanej do specyfiki konkretnej aplikacji.
Chcesz poznać naszą ofertę i zamówić części maszyn?
| Przejdź do sklepu
Przekładnie stożkowe działają poprzez zazębianie się kół zębatych ustawionych pod kątem, co umożliwia przenoszenie momentu obrotowego np. między prostopadłymi względem siebie wałami.
Koła zębate stożkowe produkuje się z materiałów takich jak stal, żeliwo, aluminium, mosiądz, miedź oraz tworzywa sztuczne.
Najważniejsze rodzaje kół zębatych stożkowych to koła proste i spiralne. Różnią się one kształtem zębów i sposobem przenoszenia napędu.
- Rodzaje łożysk i ich zastosowanie
- Łożyska przemysłowe – z jakim materiałów się je produkuje?
- Dobór łożyska do danego zastosowania
Łożyska to jedne z najważniejszych części do maszyn przemysłowych. Umożliwiają ruch obracających się oraz przesuwających się części mechanizmów, odpowiadając za efektywne przenoszenie sił i momentów obrotowych.
Łożyska stosuje się również w celu redukcji tarcia, co minimalizuje zużycie części i zmniejsza ilość energii niezbędnej do zasilania systemu przemysłowych. Ze względu na ich duże znaczenie dla działania niemal każdej maszyny przemysłowej, warto przyjrzeć im się bliżej.
Rodzaje łożysk i ich zastosowanie
Różnorodność aplikacji przemysłowych i konieczność dostosowania się do bardzo zróżnicowanych, niejednokrotnie ekstremalnych warunków wymusiły opracowanie wielu rodzajów łożysk. Najważniejsze z nich to:
- łożyska kulkowe: wykorzystywane w maszynach przemysłowych – np. w silnikach, przekładniach i elementach linii produkcyjnych. Różne rodzaje łożysk kulkowych rekomendowane są do aplikacji cechujących się niskimi obciążeniami i średnimi prędkościami obrotowymi;
- łożyska walcowe: stosowane w przekładniach i w aplikacjach wymagających dużej odporności na obciążenia. Zapewniają stabilność przy wysokich obciążeniach promieniowych;
- łożyska stożkowe: obejmują typy łożysk używanych w układach napędowych, w których wymagane są połączenia odporne na duże obciążenia osiowe;
- łożyska igiełkowe: wykorzystywane w aplikacjach o ograniczonej przestrzeni – np. w napędach liniowych. Oferują dużą nośność i precyzję przy minimalnej średnicy;
- łożyska liniowe: stosowane w układach o konstrukcji liniowej. Zapewniają precyzyjne prowadzenie i minimalizują opory ruchu;
- łożyska ślizgowe: te części maszyn sprawdzają się w miejscach o ograniczonej przestrzeni i w aplikacjach z niskimi prędkościami obrotowymi.
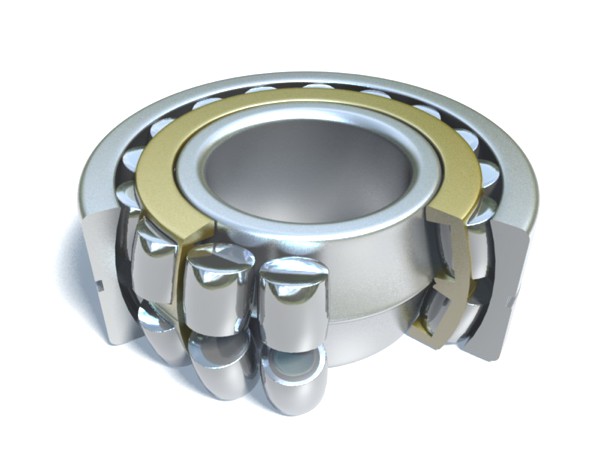
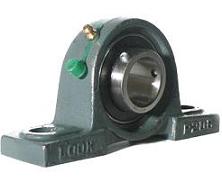
Łożyska przemysłowe – z jakim materiałów się je produkuje?
Łożyska mogą produkowane z różnych materiałów. Często jest to stal łożyskowa lub nierdzewna. Oba materiały cechują się dużą wytrzymałością na obciążenia oraz odpornością na ścieranie. Stal łożyskowa jest powszechnie używana w łożyskach standardowych, podczas gdy stal nierdzewna zastosowanie znajduje przede wszystkim w trudnych warunkach środowiskowych, panujących np. zakładach chemicznych czy spożywczych.
Oprócz metali coraz większą popularność zyskują materiały polimerowe. Wykonane z nich łożyska są lekkie, odporne na korozję i nie wymagają smarowania, dzięki czemu okazują się idealnym rozwiązaniem w środowiskach o wysokiej wilgotności lub obecności substancji chemicznych. Rzadziej spotykane są łożyska ceramiczne. Zapewniają one wyjątkową twardość, odporność na wysokie temperatury i korozję oraz niskie tarcie.
Dobór łożyska do danego zastosowania
Przy doborze łożyska konstruktor powinien wziąć pod uwagę kilka czynników: rodzaj obciążeń, prędkość obrotową, specyfikę środowiska pracy oraz wymagania co do precyzji działania. Ważne jest również uwzględnienie warunków eksploatacyjnych, takich jak temperatura lub ewentualna obecność substancji chemicznych, które mogłyby wpłynąć na trwałość i efektywność łożyska.
Dla sprawności danego połączenia i całego układu znaczenie ma nie tylko prawidłowy dobór łożyska, ale też jego utrzymanie. Dzięki regularnemu smarowaniu i kontroli stanu technicznego pomagają uniknąć przyspieszonego zużycia lub jego uszkodzenia spowodowanego przedostaniem się zanieczyszczeń. Ostateczny plan konserwacji powinien być uzależniony od rodzaju łożyska, warunków, w jakich jest ono eksploatowane oraz zaleceń producenta (związanych m.in. z materiałami, z których zostało wykonane). Nie należy zaniedbywać tego aspektu, bo odpowiednia konserwacja sprawia, że łożyska mogą działać efektywnie przez wiele lat oraz minimalizuje przestoje i koszty utrzymania.
Łożyska to ważne elementy każdej maszyny przemysłowej. Wpływają na efektywność, trwałość oraz niezawodność układu. Różnorodność dostępnych typów łożysk pozwala dobrać model odpowiedni zarówno do wymagających przekładni, jak delikatnych mechanizmów w urządzeniach precyzyjnych.
Chcesz poznać naszą ofertę i zamówić części maszyn?
| Przejdź do sklepu
W przemyśle stosuje się różne rodzaje łożysk, w tym łożyska kulkowe, walcowe, stożkowe, igiełkowe, ślizgowe i liniowe.
Łożyska produkowane są głównie ze stali łożyskowej i nierdzewnej, które zapewniają wysoką wytrzymałość i odporność na ścieranie. W nowoczesnych aplikacjach coraz częściej stosuje się ponadto lekkie, odporne na korozję i niewymagające smarowania materiały polimerowe oraz ceramikę cechującą się wysoką twardością.
Aby zapewnić długowieczność łożysk, należy regularnie je smarować i kontrolować ich stan techniczny, aby uniknąć przedostania się zanieczyszczeń. Konserwacja powinna być dostosowana do warunków eksploatacji – np. temperatury pracy układu lub obecności agresywnych substancji chemicznych.
- Sprzęgło kłowe – działanie i budowa
- Zastosowania sprzęgieł kłowych
- Sprzęgła kłowe a sprzęgła zębate
- Kłowe sprzęgła maszynowe – jak dobrać?
Sprzęgła należą do najważniejszych elementów układów przeniesienia napędu. Dzięki nim możliwe jest przeniesienie momentu obrotowego z wału czynnego (napędowego) na bierny (napędzany), a następnie na właściwe urządzenia. Zróżnicowanie budowy poszczególnych układów oraz warunków, w jakich pracują, wymusza zastosowanie różnych typów sprzęgieł. Jednym z nich – obok konstrukcji takich jak sprzęgła łubkowe czy sprzęgła oponowe – są sprzęgła kłowe. W nowym artykule wyjaśniamy, czym cechują się te części do maszyn przemysłowych i jak są one wykorzystywane.
Sprzęgło kłowe – działanie i budowa
Sprzęgło kłowe składa się z dwóch stalowych, żeliwnych lub aluminiowych piast, które są połączone elastycznym łącznikiem. Na powierzchni tych piast znajdują się charakterystyczne kły zazębiające się ze sobą i umożliwiające i tym samym przekazywanie napędu. Dzięki zaokrąglonym krawędziom kłów, sprzęgła kłowe mogą skutecznie kompensować brak osiowości między wałami bez powstawania nadmiernych nacisków.
Sprzęgła kłowe cechują się małymi rozmiarami i niewielką wagą. Mimo niskiego momentu bezwładności są w stanie przenosić wysokie momenty obrotowe. Efektywnie tłumią też drgania i redukują udary, dzięki czemu sprawdzają się w aplikacjach z nierównomierną pracą. W zależności od kąta nachylenia zębów, sprzęgła kłowe mogą pracować jako sztywne, przeciążeniowe lub jednokierunkowe.
Zastosowania sprzęgieł kłowych
Sprzęgła kłowe znajdują szerokie zastosowanie w różnych maszynach przemysłowych. Montaż tych części do maszyn przemysłowych zalecany jest między innymi w silnikach wysokoobrotowych, motoreduktorach, obrabiarkach CNC, systemach automatyki i hydrauliki siłowej, pompach, kompresorach i pakowarkach. Dobrze nadają się też do aplikacji wymagających wysokiej precyzji i niezawodności, efektywnego tłumienia drgań oraz kompensacja niewspółosiowości wałów.
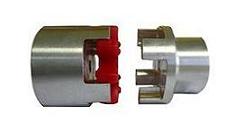

Sprzęgła kłowe a sprzęgła zębate
Podobieństwo nazw sprawia, że sprzęgła kłowe często są mylone z zębatymi. Oba rodzaje części maszyn znacznie jednak różnią się między sobą. Najważniejsza różnica tkwi w sposobie przenoszenia momentu obrotowego. W przypadku sprzęgieł kłowych napęd jest przekazywany przez zazębienie się kłów na dwóch współpracujących ze sobą tarczach. Sprzęgło zębate to rodzaj sprzęgła kompensacyjnego, które jest zdolne do kompensacji niewspółosiowości wałów.
Dzięki zaokrągleniu krawędzi kłów, sprzęgła kłowe cechują się ponadto lepszą kompensacją niewspółosiowości wałów. Sprzęgła zębate mają z kolei wyższą sztywność i przenosić wyższe momenty obrotowe. Ważną różnicą jest też to, że sprzęgła kłowe są mniejsze i lżejsze niż zębate.
Kłowe sprzęgła maszynowe – jak dobrać?
To, czy sprzęgło kłowe dobrze sprawdzi się w danej aplikacji, zależy od prawidłowego doboru tego elementu. Konstruktor układu powinien zwrócić uwagę przede wszystkim na kilka czynników. Jednym z najważniejszych jest to, jaki moment obrotowy będzie ono przenosić. Znaczenie ma także prędkość obrotowa oraz moc silnika. Równie ważne są warunki pracy – zwłaszcza temperatura otoczenia, poziom wilgotności i ewentualne narażenie na działanie agresywnych substancji. Niektóre aplikacje wymagać będą ponadto zabezpieczenia przed przeciążeniami lub możliwości szybkiego rozłączenia napędu.
Jak widać, zastosowanie odpowiednio dobranego sprzęgła kłowego pozwala na zwiększenie efektywności i niezawodności maszyny. Ich specyfika umożliwia skuteczne przenoszenie momentu obrotowego przy jednoczesnej kompensacji niewspółosiowości wałów, co czyni je idealnym wyborem w przypadku różnych aplikacji.
Chcesz poznać naszą ofertę i zamówić części maszyn?
| Przejdź do sklepu
Sprzęgła kłowe przenoszą ruch poprzez zazębienie się kłów znajdujących na dwóch piastach połączonych elastycznym łącznikiem. Zaokrąglone krawędzie kłów umożliwiają kompensację niewspółosiowości wałów, minimalizując nadmierne naciski. Dzięki temu sprzęgła tego typu skutecznie tłumią drgania i redukują udary.
Sprzęgła kłowe sprawdzają się w aplikacjach wymagających precyzji, niezawodności oraz efektywnego tłumienia drgań. Ich użycie jest też rekomendowane w systemach wymagających kompensacji niewspółosiowości wałów.
Dobór sprzęgła kłowego powinien być uzależniony od przenoszonego momentu obrotowego, prędkości obrotowej oraz mocy silnika w danej aplikacji. Ważne są też cechy takie jak możliwość pracy w określonej temperaturze i wilgotności lub odporność na agresywne chemikalia.
- Listwy zębate – najważniejsze zalety
- Zastosowania listew zębatych
- Z jakich materiałów produkuje się listwy zębate?
Listwy zębate to ważny element wielu przekładni mechanicznych. Najlepiej sprawdzą się tam, gdzie konieczne jest zapewnienie płynności i precyzji przy pracy pod dużymi obciążeniami. Jak jednak działają zębate? W jakich aplikacjach przemysłowych najczęściej są wykorzystywane? Więcej na ten temat piszemy w nowym artykule.
Listwy zębate – najważniejsze zalety
W przekładniach, w których wykorzystuje się listwy zębate, ruch obrotowy jest zamieniany na ruch posuwisty lub na odwrót. Umożliwia to precyzyjne sterowanie maszyną i wydajne przenoszenie napędu w różnych aplikacjach. Rozwiązania tego typu spotykane są zarówno w urządzeniach do użytku codziennego, jak i w wysoko wyspecjalizowanych maszynach przemysłowych. Różnorodność zastosowań listew zębatych to wynik nie tylko specyfiki opartych na nich przekładni, ale też wysokiej jakości tych podzespołów, dzięki którym możliwe jest ich użycie nawet w najtrudniejszych warunkach.
Szerokie rozpowszechnienie listew zębatych jest efektem licznych zalet tej technologii. Do najważniejszych należy zaliczyć:
- duża sztywność umożliwiająca stabilne przenoszenie napędu, nawet przy dużych obciążeniach;
- wysoka precyzja – układy oparte o listwy zębate pracują z dużą dokładnością, co ma duże znaczenie w wymagających aplikacjach przemysłowych;
- doskonała wydajność – listwy zębate umożliwiają uzyskanie wysokich prędkości przesuwu przy jednoczesnym zachowaniu precyzji i wytrzymałości;
- modularność – listwy można łatwo dostosowywać do zmieniających się potrzeb i warunków użytkowania, wymieniać uszkodzone lub przestarzałe części oraz rozbudowywać lub modyfikować system w zależności od wymagań;
- możliwość doboru przełożenia – zawierający koła zębate katalog jest na tyle zróżnicowany, że bez problemu można dobrać odpowiedni model do listwy i stworzyć przełożenie dostosowane do specyfiki danej aplikacji.
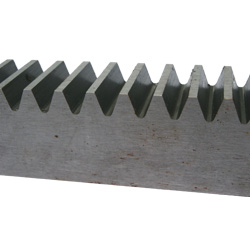
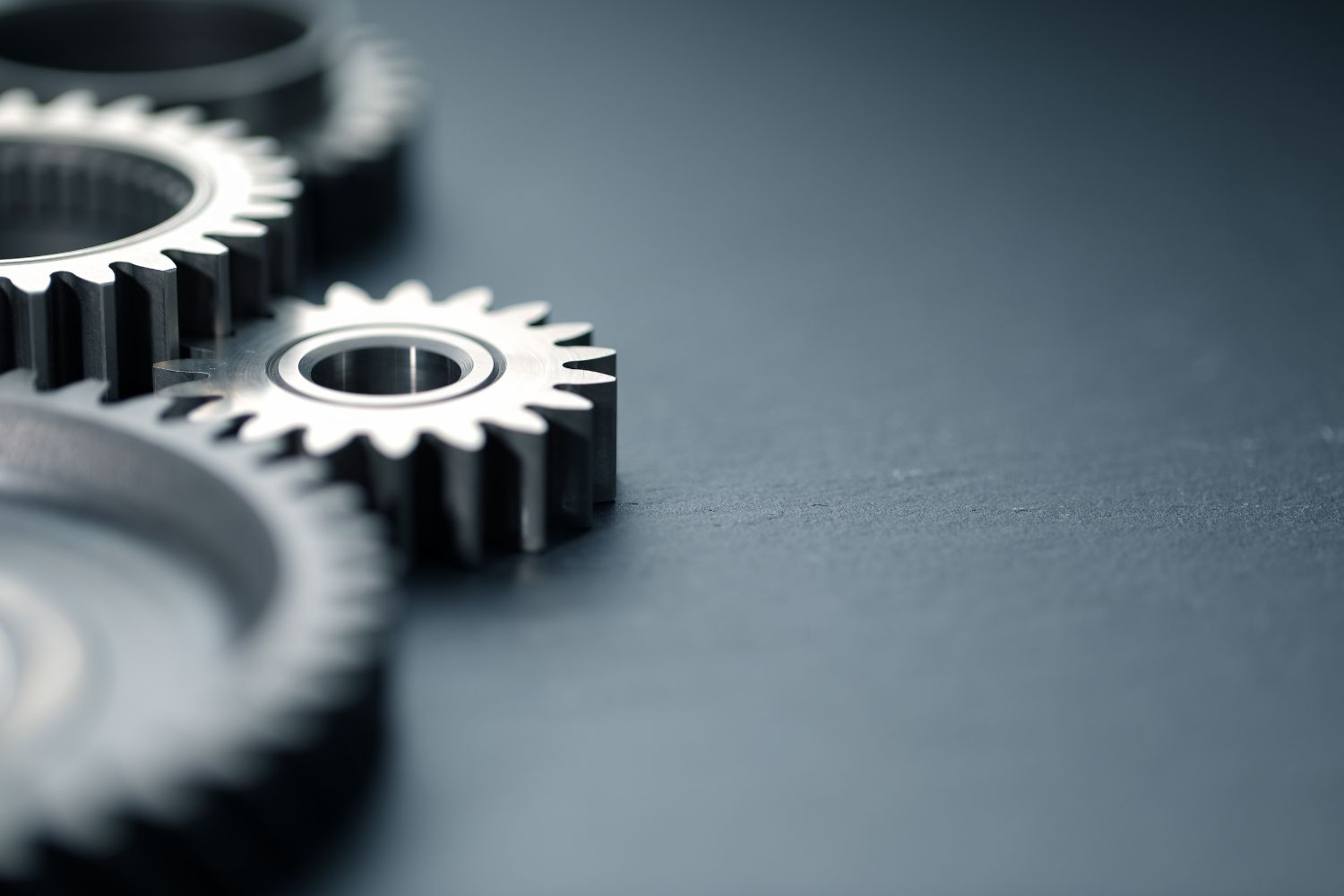
Zastosowania listew zębatych
Listwy zębate są powszechnie stosowane w przemyśle – przede wszystkim w maszynach do obróbki metali takich jak wiertarki stołowe czy tokarki mechaniczne. W tych pierwszych umożliwiają opuszczanie trzpienia wiertarki wraz z wiertłem i tym samym kontrolę czasu obróbki materiału. W tokarkach mechanicznych mechanizm oparty o listwę zębatą jest z kolei wykorzystywany do precyzyjnego przesuwu narzędzia. Ich odporność na korozję i działanie czynników chemicznych oraz brak konieczności częstego smarowania sprawiają, że są one również idealnym rozwiązaniem w środowiskach wymagających wysokiej wytrzymałości i niezawodności. Stosuje się je np. myjniach lub maszynach do pakowania żywności.
Listwy zębate znajdują również szerokie zastosowanie poza przemysłem – zwłaszcza w urządzeniach, od których wymaga się cichej pracy. Najlepszy przykład to automatyczne napędy bramowe, w których listwy tego typu zapewniają płynny i cichy przesuw bramy wjazdowej.
Z jakich materiałów produkuje się listwy zębate?
Dla wytrzymałości i wydajności przekładni wykorzystujących listwy zębate duże znaczenie ma to, z jakich materiałów są one wykonane. Najczęściej produkuje się je z odpowiednio wyselekcjonowanych gatunków stali – np. C 45. Zapewnia to wytrzymałość niezbędną do efektywnego przenoszenia napędu w różnych aplikacjach przemysłowych. Stalowa konstrukcja listw zębatych charakteryzuje się wysoką twardością oraz odpornością na duże obciążenia i umożliwia ich użycie w maszynach do obróbki metali.
Listwy zębate coraz częściej są też produkowane z tworzyw sztucznych – przede wszystkim z technopolimerów na bazie poliamidu wzmocnionych włóknem szklanym. Materiały tego typu cechują się wysoką wytrzymałością mechaniczną oraz odpornością na różne czynniki środowiskowe, co czyni je atrakcyjną alternatywą dla tradycyjnej stali. Są również znacznie lżejsze niż stal, co ma duże znaczenie w aplikacjach wymagających ograniczenia masy.
Jak widać, listwy zębate to ważne elementy wielu różnych przekładni mechanicznych. Umożliwiają przenoszenie napędu z dużą efektywnością i precyzją. Ich zastosowanie w różnych typach przekładni pozwala na efektywne wykorzystanie energii i zapewnia niezawodność w działaniu maszyn przemysłowych. Dzięki nim konstruktorzy mogą osiągnąć wymaganą sprawność różnych aplikacji, co z kolei przekłada się na poprawę parametrów linii produkcyjnej i zwiększenie konkurencyjności zakładu.
Chcesz poznać naszą ofertę i zamówić części maszyn?
| Przejdź do sklepu
Listwy zębate – obok kół zębatych – są elementami przekładni zmieniających ruch obrotowy na posuwisty.
Przekładnie zbudowane z użyciem listw zębatych znajdują zastosowanie m.in. w obrabiarkach (tokarka, frezarka, wiertarka stołowa), napędach do bram automatycznych, urządzeniach drukarskich czy maszynach z branży spożywczej (do pakowania żywności, przenośnikach, owijarkach) oraz rolnej.
Najważniejszym materiałem do produkcji listew zębatych jest stal węglowa o dużej wytrzymałości (np. gatunek C 45). Obecnie spotykane są też listwy z tworzyw sztucznych.
- Produkcja niestandardowych części maszyn z pomocą CNC
- Jakie materiały można przetwarzać metodą CNC?
- Zastosowanie zaawansowanych technik obróbki CNC
Obrabiarki CNC cieszą się dziś ogromną popularnością. Rewelacyjnie sprawdzają się zarówno przy produkcji jednostkowej, jak i wielkoseryjnej. Jednak prawdziwe możliwości wykazują one przy produkcji niestandardowych i skomplikowanych detali: części maszyn oraz prototypów. Na korzyść frezarek i tokarek CNC działa też możliwość obrabiania wielu, całkowicie różnych materiałów. Jesteś ciekaw, co można uzyskać metodami obróbki skrawaniem ze wspomaganiem komputerowym? Sprawdź poniżej!
Produkcja niestandardowych części maszyn z pomocą CNC
Pierwsza obrabiarka CNC powstała w 1952 roku i była sterowana z pomocą kodowanych binarnych taśm dziurkowanych. Od tego czasu technologia komputerowa mocno się rozwinęła, a możliwości urządzeń CNC są znacznie większe. Ich zalety widoczne są szczególnie przy produkcji niestandardowych części maszyn.
- Błyskawiczne wdrożenie. Tworzenie programu odbywa się na podstawie gotowego modelu CAD, a skomplikowane ścieżki tworzone są automatycznie przez algorytmy komputerowe. W ten sposób zaprojektowanie kolejnych operacji wymaga znacznie mniej czasu.
- Eliminacja błędów na etapie tworzenia programu. Uruchomienie cyfrowej symulacji pozwala na wykrycie większości błędów, w szczególności kolizji obrabianego elementu oraz narzędzia. Dzięki temu nie trzeba wykonywać wielu kosztownych prób. W wielu przypadkach już pierwszy wykonany detal mieści się w założonych tolerancjach.
- Obróbka skomplikowanych kształtów. Nowoczesne obrabiarki CNC mogą działać nawet w 9 osiach. Takie urządzenia są w stanie wykonywać nawet najbardziej skomplikowane detale, niedostępne dla tradycyjnych frezarek czy tokarek.
- Wysoka dokładność i precyzja. Wszystkie ruchy wykonywane są z komputerową precyzją, co zapewnia bardzo wysoką powtarzalność wymiarową produkowanych detali przy zachowaniu niewielkich odchyłek.
- Niskie koszty. Ograniczenie czasu wdrożenia oraz niskie ryzyko błędów przekłada się na istotne oszczędności całego procesu. Szczególnie w przypadku niestandardowych części maszynowych.
Wspomniane zalety sprawiają, że obrabiarki CNC doskonale sprawdzają się zarówno w produkcji jednostkowej (krótki czas wdrożenia i minimalizacja błędów programu już na etapie projektu), jak i masowej (duża dokładność i powtarzalność).

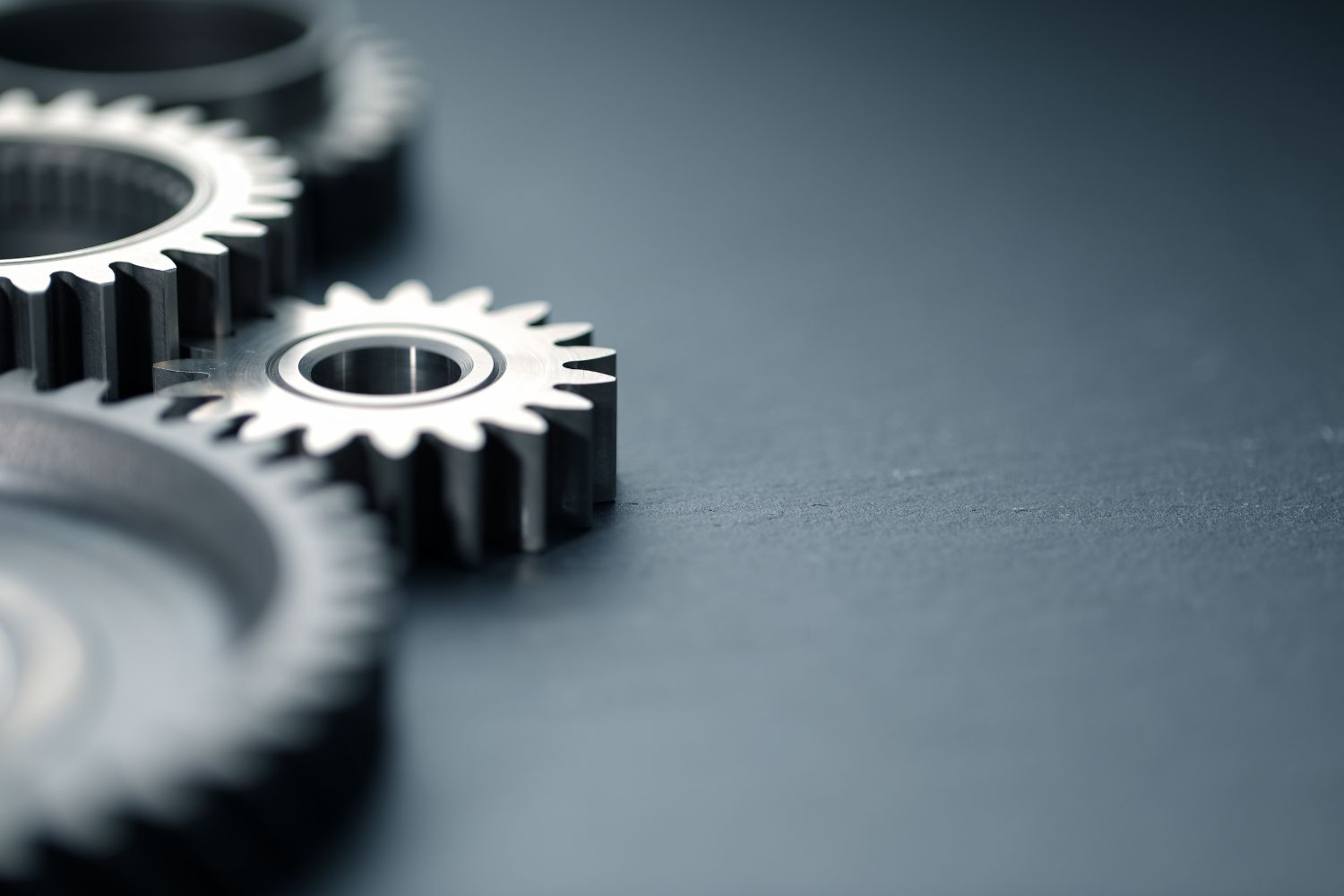
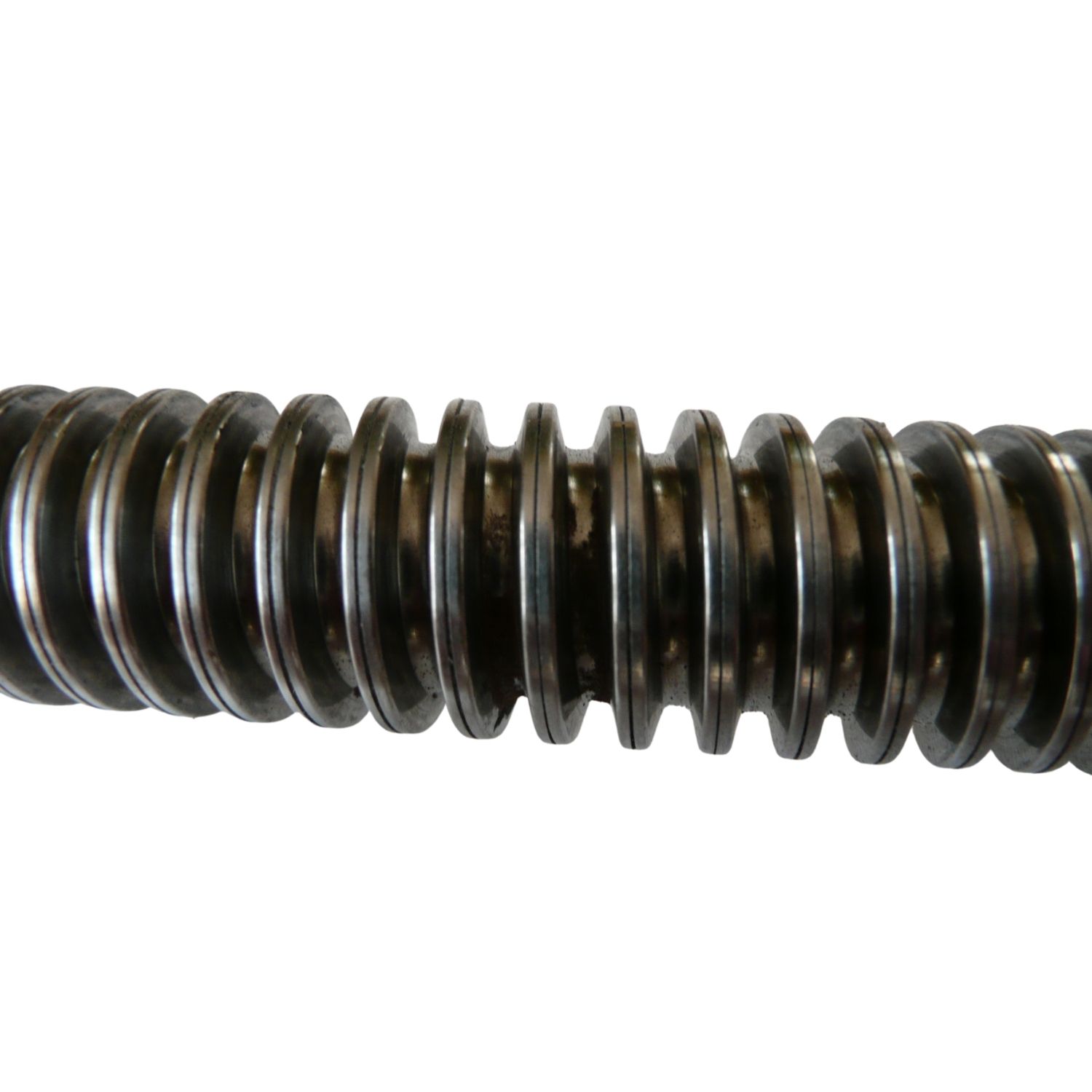
Jakie materiały można przetwarzać metodą CNC?
Podstawowym materiałem, wykorzystywanym do wytwarzania części maszyn za pomocą obrabiarek CNC, jest nadal stal. Wykorzystuje się różne gatunki tego materiału, w zależności od oczekiwanych parametrów gotowego detalu. Przykładowo koła zębate wykonuje się przeważnie ze stali C45, natomiast łańcuchy przemysłowe ze stali nierdzewnej, czarnej lub Hardox. Elementy żelazne cechują się dobrą sprężystością i dużą wytrzymałością. Część gatunków (głównie stal chromowa) jest również odporna na korozję.
Obrabiarki CNC dobrze radzą sobie także z obróbką aluminium. Optymalny stosunek wytrzymałości do wagi sprawia, że jest to materiał powszechnie wykorzystywany w branży automotive (np. koła pasowe zębate), lotniczej oraz kosmicznej. Znacznie rzadziej w tych branżach wytwarza się detale tytanowe, jednak te mają często kluczowe znaczenie.
W ostatnich latach coraz częściej stosuje się części maszyn z tworzywa sztucznego. Przykładem mogą być koła zębate modułowe, charakteryzujące się wysoką odpornością na skręcanie. Są one również bardzo wytrzymałe pod kątem zmęczeniowym. Wykonuje się je na obrabiarkach CNC z tworzywa termoplastycznego Nylon PA6 z domieszką włókna szklanego (30%).
Z maszyn CNC korzysta także przemysł meblarski oraz inne, opierające produkcję na materiale drewnianym.
Zastosowanie zaawansowanych technik obróbki CNC
W obrabiarkach CNC bardzo ważna jest wysoka precyzja wykonywanych ruchów. Dlatego też wykorzystywane są do tego śruby trapezowe. Choć charakteryzują się one nieco niższą sprawnością (z powodu wyższego tarcia), zapewniają wyjątkową dokładność w połączeniu ze sterowaniem komputerowym. Sprawiają one, że nowoczesna frezarka nie musi pracować tylko w trzech osiach (ruch po płaszczyźnie XY oraz posuw w osi pionowej Z), ale również w dodatkowych osiach. Wykorzystując dodatkowo obrót narzędzia, produkuje się koła zębate stożkowe.
W przypadku niestandardowych części maszynowych warto wyposażyć się w dociski szybkomocujące, które znacznie ułatwiają instalację detalu w obszarze roboczym. W takim przypadku koniecznie należy uwzględnić mocowanie w programie CAM. Jak dokładnie wygląda obróbka skrawaniem CNC, pisaliśmy w innym artykule. Podobne metody stosuje się w przypadku skomplikowanych części maszynowych.
Chcesz poznać naszą ofertę i zamówić części maszyn?
| Przejdź do sklepu
Główne zalety to błyskawiczne wdrożenie projektu dzięki automatycznemu tworzeniu ścieżek narzędzi, wysoka dokładność i precyzja obróbki, możliwość obróbki skomplikowanych kształtów, eliminacja błędów na etapie projektowania oraz niskie koszty produkcji dzięki minimalizacji ryzyka błędów i szybkiemu czasowi wdrożenia.
Metodą CNC można przetwarzać szeroki zakres materiałów, w tym różne gatunki stali, aluminium, tworzywa sztuczne takie jak Nylon PA6 z domieszką włókna szklanego, a także materiały drewniane.
W obrabiarkach CNC stosuje się zaawansowane techniki, takie jak obróbka w wielu osiach (nawet do 9 osi), wykorzystanie śrub trapezowych dla zwiększenia dokładności czy dociski szybkomocujące ułatwiające instalację detali.
- Stal w produkcji maszyn. Kiedy jest wykorzystywana?
- Zastosowanie stali nierdzewnej w produkcji maszyn
- Aluminium w przemyśle maszynowym. Lekkie i trwałe
- Mosiądz i brąz w produkcji części do maszyn
- Tworzywa sztuczne w produkcji części maszynowych
Dobór materiałów do produkcji maszyn przemysłowych jest jednym z najważniejszych aspektów ich projektowania. Jakie rozwiązania mają do dyspozycji konstruktorzy?
Części maszyn muszą spełniać określone zadania. Pracują często w trudnych środowiskach, o dużym poziomie wilgoci i w kontakcie z agresywnymi substancjami. Poddawane są też ogromnym obciążeniom, co w połączeniu z pracą w trybie ciągłym może prowadzić do przyspieszonego zużywania poszczególnych elementów. Dlatego tak ważny jest dobór odpowiednich materiałów do ich wykonania. W nowym artykule omawiamy materiały, które we współczesnym przemyśle maszynowym mają największe znaczenie.
Stal w produkcji maszyn. Kiedy jest wykorzystywana?
Stal w różnych gatunkach to podstawowy materiał stosowany w produkcji części do maszyn przemysłowych. Za jej zastosowaniem przemawia wiele argumentów – jednym z najważniejszych jest trwałość. Nowoczesne stopy i gatunki stali cechują się wysoką odpornością na odkształcenia i pęknięcia, dzięki czemu możliwe jest np. zastosowanie ścianek o mniejszej grubości i tym samym redukcja masy poszczególnych elementów oraz całych maszyn.
Coraz większe znaczenie mają także aspekty ekonomiczne i ekologiczne. Stal z łatwością poddaje się recyklingowi, co czyni jej produkcję bardzo opłacalną. Długi cykl życia produktu przekłada się z kolei na niską emisyjność. Emisja gazów cieplarnianych mierzona jako ekwiwalent CO2 przy produkcji stali wynosi zaledwie 2-2,5 tys. kilogramów na tonę (dla porównania – w przypadku aluminium to 16,5 tys. kilogramów). Szerokie stosowanie stali umożliwia więc producentom i całym gospodarkom dostosowanie do limitów emisji.
Zastosowanie stali nierdzewnej w produkcji maszyn
Na rynku dostępnych jest wiele gatunków stali nierdzewnej. Każda z nich ma nieco odmienne właściwości, ale łączy je duża wytrzymałość na korozję, umożliwiająca zastosowanie do budowy maszyn pracujących w agresywnych środowiskach. W przemyśle maszynowym najczęściej stosuje się następujące rodzaje stali nierdzewnej:
- austenityczne (np. AISI 304, AISI 316): popularne i tanie w produkcji stopy, wykorzystywane m.in. do produkcji obudów;
- ferro-martensytne (np. AISI 410, AISI 420): dzięki wysokiej zawartości węgla, stopy tego typu cechują się większą odpornością na zużycie. W przemyśle maszynowym znajdują zastosowanie np. w produkcji łożysk i części takich jak pręty gwintowane śruby trapezowe nierdzewne;
- duplex (np. AISI 2205) i precypitatywne (np. AISI 17-4 PH): łączą w sobie właściwości obu poprzednich typów. Duża odporność na zużycie w połączeniu z niską zawartością węgla (a co za tym idzie, mniejszą podatnością na korozję), sprawiają, że stopy te są używane do produkcji maszyn na potrzeby najbardziej wymagających sektorów – np. przemysłu chemicznego.
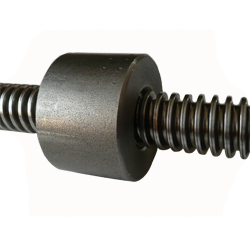
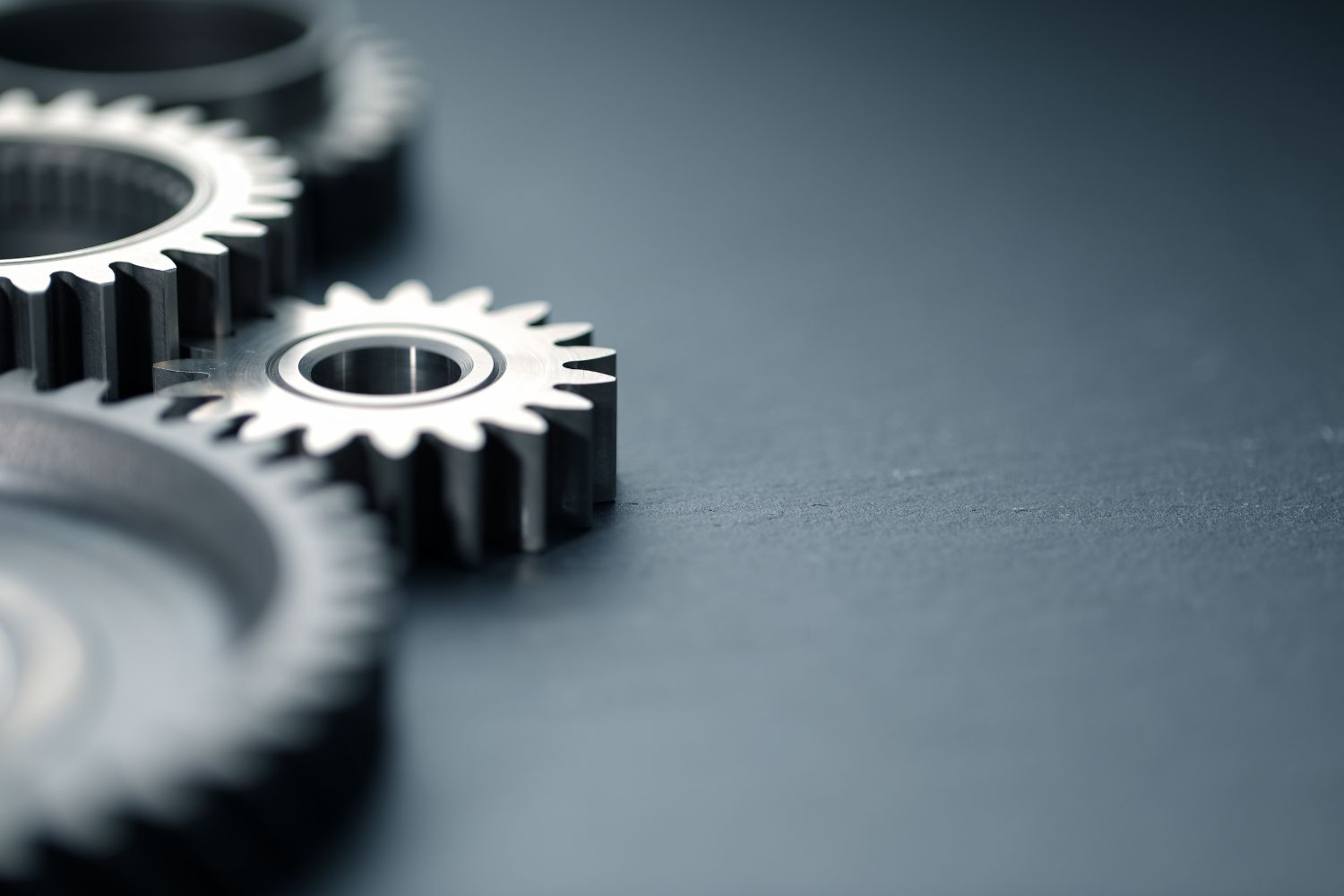
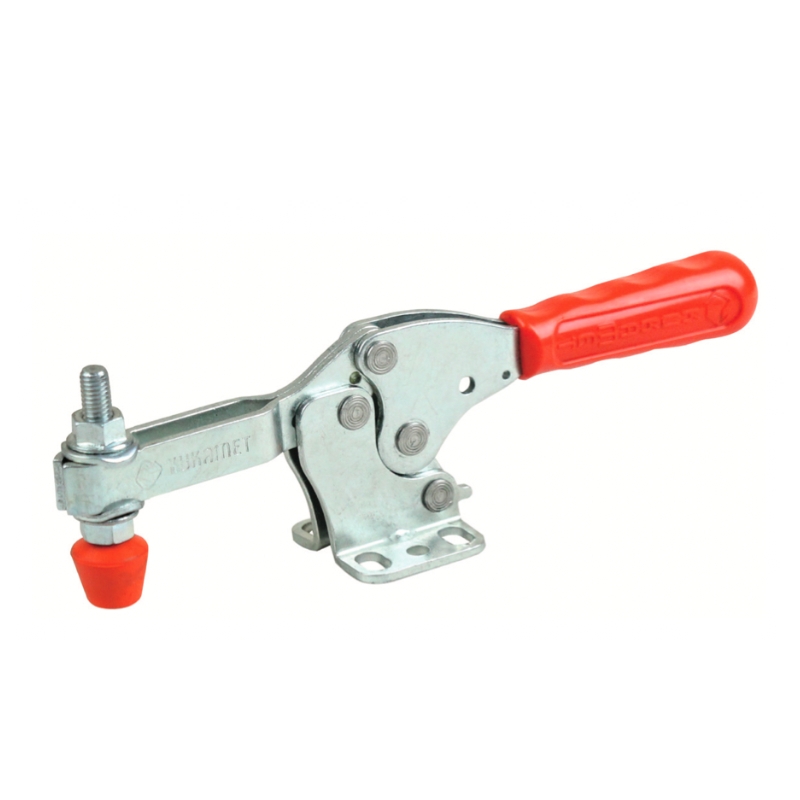
Aluminium w przemyśle maszynowym. Lekkie i trwałe
Obok stali, aluminium to często stosowany materiał do produkcji części maszyn. O jego popularności decyduje połączenie trzech czynników – niskiej gęstości, małej podatności na korozję i dużej wytrzymałości mechanicznej (zwłaszcza po obróbce cieplnej). Wykonane z niego elementy są lekkie, a jednocześnie dobrze radzą sobie w kontakcie z agresywnymi substancjami oraz dużymi obciążeniami, wstrząsami lub uderzeniami. W produkcji maszyn zastosowanie znajduje przede wszystkim aluminium serii 2000. Zalicza się do niej stopy zawierające miedź, mangan i magnez. Mimo że mają one mniejszą odporność na korozję, to cechują się dużą wytrzymałością na uszkodzenia.
Mosiądz i brąz w produkcji części do maszyn
Kolejna grupa materiałów wykorzystywanych w przemyśle maszynowym to stopy miedzi – brąz i mosiądz. Jeśli chodzi o pierwszy stop, w tym sektorze najczęściej stosowane są: brąz cynowy (do produkcji elementów sprężystych i trudnościeralnych, poddawanych dużym obciążeniom, takich jak łożyska i układ przeniesienia napędu), aluminiowy (wały napędowe), oraz krzemowo-cynkowo-manganowy (napędy). Mosiądz wykorzystywany do produkcji maszyn to przede wszystkim stop CuZn37Mn3Al2PbSi (CW713R), wykorzystywany do produkcji np. łożysk ślizgowych.
Tworzywa sztuczne w produkcji części maszynowych
Przemysł maszynowy korzysta przede wszystkim ze stopów metali, ale w ostatnich latach notuje się wzrost popularności lekkich tworzyw sztucznych. Nowoczesne materiały tego typu są bardzo wytrzymałe mechanicznie i odporne na korozję. Łatwość obróbki umożliwia wydajną i precyzyjną produkcję nawet najbardziej wymagających detali, a korzystny stosunek masy do parametrów użytkowych pozwala zmniejszyć wagę poszczególnych elementów. Ważną zaletą części maszyn z komponentów jest też możliwość pracy bez konieczności smarowania. Tworzywa sztuczne wykorzystywane są ponadto do produkcji rękojeści i innych elementów np. w dociskach szybkomocujących.
Różnorodność materiałów pozwala producentom maszyn na dostosowanie swoich produktów do specyfiki danej aplikacji. Przemysł maszynowy, dążąc do efektywności i zrównoważonego rozwoju, nieustannie poszukuje nowych technologii i materiałów, które pozwolą na tworzenie wydajnych, trwałych i ekologicznych rozwiązań – zapewne w najbliższych latach będą więc pojawiać się kolejne materiały.
Chcesz poznać naszą ofertę i zamówić części maszyn?
| Przejdź do sklepu
Części maszyn powinny być wytwarzane z materiałów spełniających określone wymagania w zależności od przeznaczenia danego elementu np. wytrzymałość mechaniczną, odporność na korozję, odporność na agresywne substancje. Inny materiał będzie wykorzystany do produkcji wału napędowego a inny do obudowy.
W przemyśle maszynowym najczęściej korzysta się z różnych stopów stali, aluminium, brązu i mosiądzu. Rośnie też znaczenie nowoczesnych tworzyw sztucznych.
Stal od dziesięcioleci jest jednym z najważniejszych materiałów do produkcji części maszynowych. Poza jej właściwościami fizycznymi i chemicznymi (stopy nierdzewne), w ostatnich latach na ten stan rzeczy wpływa też łatwość jej ponownego przetworzenia i wynikające z niej korzyści ekologiczne oraz ekonomiczne.
- Uwaga, czyli wyposażenie pod kontrolą
- Podstawy konserwacji maszyn przemysłowych
- Automatyka, czyli na straży jakości
Pojawiające się uszkodzenia części do maszyn przemysłowych są powodem niezwykle poważnych konsekwencji dla każdego zakładu pracy. Warto bowiem podkreślić, że potencjalne przerwy w produkcji to jedynie początek piętrzących się komplikacji. Właściciel przedsiębiorstwa musi brać pod uwagę spore koszty powstałej awarii, utratę dochodów, zwiększone ryzyko niebezpiecznych incydentów, a co najważniejsze – brak możliwości realizacji zleceń i utratę wiarygodności. Jak temu zapobiec? Czasem wystarczy zidentyfikować te części maszyn, które wymagają szczególnej uwagi!
Uwaga, czyli wyposażenie pod kontrolą
Na wstępie warto podkreślić, że cykliczne uszkodzenia i dysfunkcje nie muszą wynikać z niskiej jakości produktów lub wad fabrycznych, ale bardzo wymagających warunków pracy. Zatem, jakie części maszyn zasługują na regularną kontrolę stanu eksploatacji?
Pierwszym elementem są łożyska, tak fundamentalne dla wielu niezawodnych urządzeń produkcyjnych, ponieważ są odpowiedzialne za skuteczną pracę wałów i innych części ruchomych. Nieprawidłowości mogą wynikać z przenikających do wnętrza zabrudzeń, ale również nieprawidłowego procesu montażu. Innym źródłem defektu jest także błędne ustawienie i dopasowanie oraz postępująca korozja poszczególnych obszarów łożyska. Jakie inne elementy parku maszynowego mogą wykazywać podobne objawy?
Tutaj należy wymienić wszelkiego rodzaju koła zębate, które jako elementy przekładni zębatych narażone są na wiele uszkodzeń, co wynika bezpośrednio z mechanizmu i charakteru ich aktywności. Należące do tej grupy koła zębate modułowe lub koła pasowe zębate doświadczają licznych deformacji i naruszenia segmentów. Bardzo ważną kwestią w kontekście stosowania opisywanych ogniw jest spójność i kompatybilność wszystkich składników. Co to oznacza w praktyce? Zdarza się, że serwis wymaga szybkiej wymiany koła zębatego. Jednak osoba odpowiedzialna za taką obsługę urządzenia zapomina o wymianie już mocno zużytych śrub. W rezultacie cały system przekładni ulega szybkiemu poluzowaniu, a to prowadzi do uszkodzenia samego ogniwa, ale również kosztownej aparatury. Jakie praktyki zapewnią zatem wydajne, efektywne i bezpieczne działanie parku maszynowego?
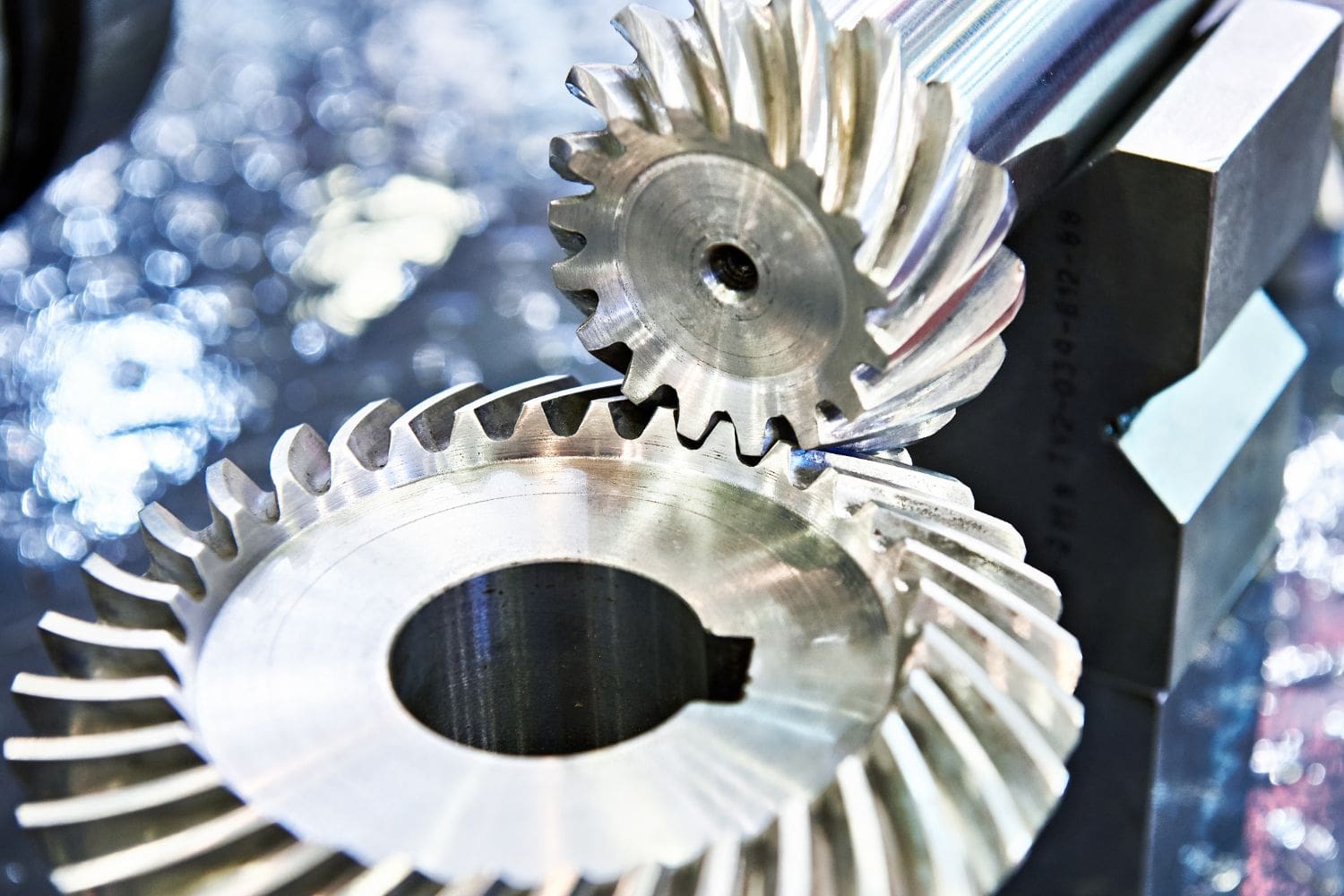
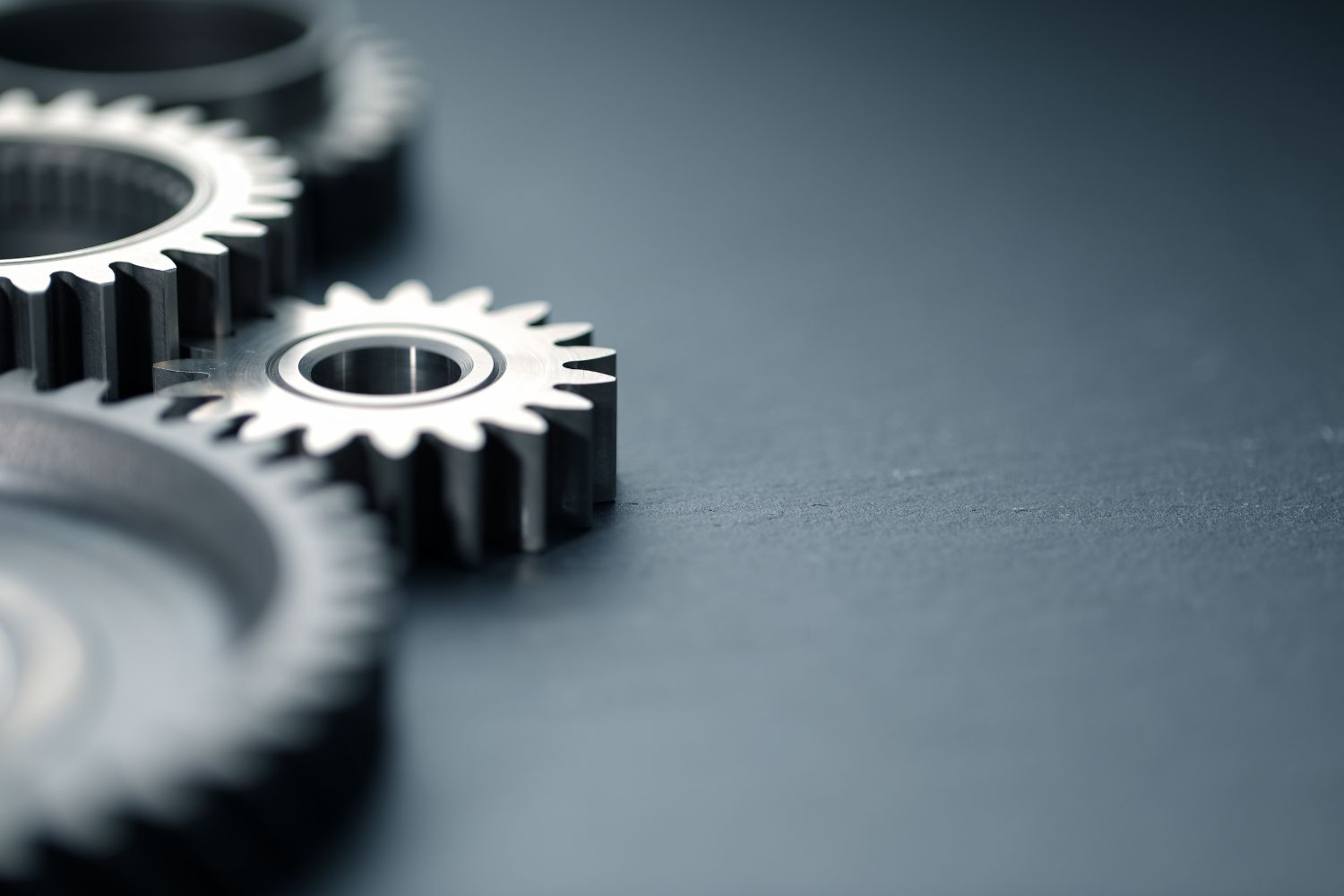
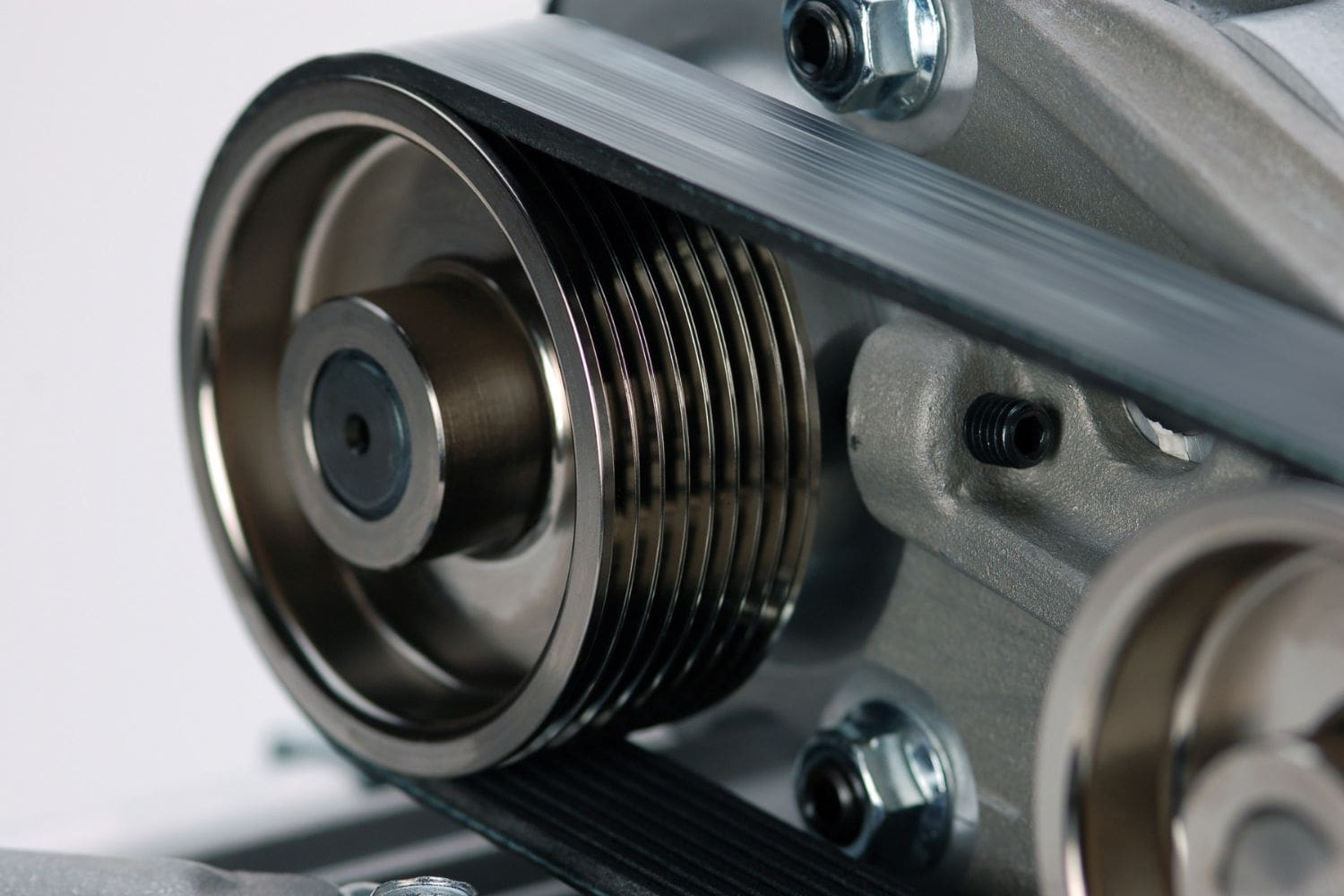
Podstawy konserwacji maszyn przemysłowych
Istnieje jednak kilka prostych i szablonowych metod, które zagwarantują idealne warunki do działania. Dbałość i troska o regularną realizację kluczowych czynności zapobiega szybkiemu zużyciu się elementów. Jakie to akcje?
Smarowanie
Smarowanie poszczególnych elementów wpływa na długowieczność stosowanych urządzeń. Odpowiednie substancje skutecznie redukują powstające tarcie, co chroni przed widocznym zużyciem. Dodatkowo, profesjonalne produkty dbają o utrzymanie właściwych warunków termicznych oraz asekurują przed wpływem negatywnych procesów, takich jak korozja. To jednak nie wszystko!
Smarowanie czułych obszarów części maszyn uszczelnia całe środowisko i optymalizuje pracę kooperujących segmentów. Jest to zatem niezbędne narzędzie każdego odpowiedzialnego zakładu przemysłowego.
Regularna inspekcja
Drugi filar niezawodnego środowiska pracy podkreśla znaczenie systematycznych kontroli. Takie praktyki dotyczą sprawdzania potencjalnych luzów, stopnia zużycia wszelkich śrub, wałów, przegubów oraz ich osłon, łańcuchów rolkowych, napinaczy, głowic, pasów klinowych, ale również kondycji istniejących przewodów elektrycznych lub czujników zaawansowanych układów.
Rzetelnie zrealizowana kontrola zwraca także uwagę na czystość narzędzi pracy. Nawet drobne zanieczyszczenia mogą być powodem naprawdę wielkich problemów w późniejszym czasie. Co więcej, weryfikacja dostępnych przyrządów powinna sprawdzać kwestię potencjalnych przeciążeń. Bowiem to przekraczanie dopuszczalnych norm jest powodem licznych awarii.
Jak widać, systematyczność wdrażanych modernizacji determinuje stan i efektywność wielu hal przemysłowych. Czy istnieje sposób na uproszenie tych procedur?
Automatyka, czyli na straży jakości
Zdecydowanie, a odpowiedzią jest automatyka. Instalacja wyspecjalizowanej aparatury umożliwia nieustanny nadzór nad najważniejszymi parametrami i właściwościami sprzętu. Innowacyjna technologia analizuje zebrane dane, co pozwala przewidzieć moment wymaganego serwisu. Wiele nowoczesnych maszyn posiada opcję samoczyszczenia oraz ewaluacji aktualnego stanu, a także łatwą integrację urozmaiconych systemów. Tak kompleksowy zakres działania gwarantuje gotowość do pracy, bez względu na skalę i format działalności!
Chcesz poznać naszą ofertę i zamówić części maszyn?
| Przejdź do sklepu
Warto kontrolować stan łożysk, kół zębatych, ale również wszelkich podzespołów.
Kluczowe jest tutaj smarowanie oraz systematyczna kontrola techniczna.
Zaawansowane technologie analizują zgromadzone dane, co umożliwia wyznaczenie idealnego momentu na serwis.
- Koła zębate modułowe – budowa i działanie
- Co wyróżnia dobre koła zębate modułowe?
- Na co zwrócić uwagę przy wyborze części do maszyn przemysłowych?
Koła zębate modułowe to elementy przenoszenia napędu, które są stosowane w wielu maszynach i urządzeniach. Jak wygląda ich budowa? Czym charakteryzują się dobre koła zębate modułowe? Odpowiedzi na te i inne pytania znajdują się w niniejszym artykule.
Koła zębate modułowe – budowa i działanie
Koła zębate modułowe to termin określający koła zębate walcowe o zębach prostych. Są one zbudowane z wieńca zębatego, zębów oraz piasty, a sposób ich budowy niewątpliwie wpływa na optymalizację pracy poszczególnych części maszyn. W jaki sposób działają koła zębate modułowe? Otóż, istotne w tym przypadku jest to, że zęby koła mogą zarówno pełnić rolę aktywatora ruchu obrotowego, jak i przenosić ruch przy wykorzystaniu współdziałania dodatkowych elementów. Może to być nie tylko listwa zębata, ale również samo koło, dzięki czemu stanowi ono element przenoszący ruch obrotowy.
W kontekście kół zębatych modułowych istotne jest oczywiście ich dopasowanie do konkretnego mechanizmu przenoszenia ruchu. Warto zatem wiedzieć to, że koła zębate modułowe klasyfikuje się między innymi ze względu na budowę, co pozwala wyróżnić koła zębate z piastą lub bez piasty. Podziału dokonuje się również ze względu na moduł, czyli określenie wielkości koła zębatego, które obejmuje jego średnicę oraz ilość zastosowanych zębów. Pozwala to wyróżnić koła zębate oznaczone symbolami 1; 1,5; 2; 2,5; 3; 4; 5; 6 oraz 8, co pozwala dopasować wielkość modułu do danego mechanizmu przenoszenia ruchu. Szczegółowe wymiary poszczególnych kół pozwala sprawdzić koła zębate katalog.
Co wyróżnia dobre koła zębate modułowe?
Zaletą kół zębatych modułowych jest precyzja wykonania czy kompatybilność, która przekłada się na łatwość ich wymiany oraz brak konieczności przeprowadzania modyfikacji w mechanizmie przenoszenia ruchu. Co zatem jeszcze wyróżnia dobre koła zębate modułowe? Otóż, istotna jest w tym przypadku między innymi ich wydajność oraz odporność na duże obciążenia, dzięki którym koła zębate tego typu gwarantują efektywne przenoszenie napędu bez konieczności częstej wymiany. Atutem jest również wszechstronne zastosowanie, ponieważ koła zębate modułowe sprawdzają się nie tylko jako części do maszyn przemysłowych, ale są również wykorzystywane w samochodach osobowych i ciężarowych, czy maszynach budowlanych i rolniczych. Poza tym ich zaletą jest cicha, stabilna i płynna praca, co w połączeniu z niezawodnością przekłada się na doskonałe warunki użytkowania. Zastosowanie kół zębatych modułowych w przekładniach gwarantuje nie tylko generowanie niższego poziomu hałasu, ale także skuteczne tłumienie pojawiających się drgań, czy niwelowanie wibracji.
Na co zwrócić uwagę przy wyborze części do maszyn przemysłowych?
Wybierając części do maszyn przemysłowych, takie jak np. koła zębate modułowe warto zwrócić uwagę na kilka istotnych kwestii. Najważniejszą jest oczywiście ich odpowiednie dopasowanie zarówno do zastosowania, jak i konstrukcji danej maszyny. W związku z tym warto skorzystać z doradztwa świadczonego przez dostawcę oraz skorzystać z udostępnianych przez niego materiałów, których przykładem może być koła zębate katalog. Istotną kwestią jest także jakość wykonania części maszyn, co powoduje, że warto wybierać wyłącznie produkty renomowanych firm. Gwarantuje to nie tylko odpowiednią pracę części maszyn, ale również ich długą żywotność. Jest to ważne z punktu widzenia ewentualnych awarii, których wystąpienie może skutkować przestojem, a co za tym idzie poniesieniem dodatkowych kosztów. W związku z tym warto zwrócić także uwagę na dostępność części maszyn oferowaną przez ich dostawcę, ponieważ umożliwi to szybkie usuwanie ewentualnych usterek.
Podsumowując, należy stwierdzić, że dobre koła zębate modułowe to części maszyn, które zapewniają odpowiednią wydajność nawet w najtrudniejszych warunkach pracy. W efekcie wykorzystuje się je w wielu różnych maszynach i urządzeniach, gdzie odpowiadają za przekazanie napędu.
Chcesz poznać naszą ofertę i zamówić części maszyn?
| Przejdź do sklepu
Istotny w tym przypadku jest jego rodzaj (z piastą lub bez piasty) oraz wielkość modułu, a sam dobór ułatwia koła zębate katalog.
Koła zębate modułowe to części maszyn przemysłowych, budowlanych i rolniczych. Zastosowanie znajdują również w silnikach samochodów osobowych i ciężarowych.
Koło zębate modułowe składa się z wieńca, zębów o określonej szerokości oraz opcjonalnie piasty.
- Dociski szybkomocujące dla przemysłu i rzemiosła
- Czemu warto stosować dociski szybkomocujące?
- Dobór docisków szybkomocujących. Na co zwrócić uwagę?
- Dociski szybkomocujące – precyzyjna i bezpieczna praca
Zastosowanie docisków szybkomocujących ma duże znaczenie z punktu widzenia bezpieczeństwa i wydajności pracy. Co warto wiedzieć o tego typu sprzęcie?
Spawanie, obróbka materiałów, serwisowanie pojazdów czy prace przy linii montażowej – to tylko niektóre z zadań wymagających precyzyjnego i niezawodnego unieruchomienia elementów. W warunkach zakładu przemysłowego lub warsztatu rzemieślniczego w tym celu doskonale sprawdzają się dociski szybkomocujące. Jakie zastosowania znajdują dociski? Jak dobrać modele dostosowane do potrzeb danego zakładu?
Dociski szybkomocujące dla przemysłu i rzemiosła
Dociski szybkomocujące to ważny element wyposażenia zakładów produkcyjnych i warsztatów. Są stosowane przede wszystkim w tych branżach, w których duże znaczenie ma precyzja i bezpieczeństwo prac. Ich przeznaczeniem jest mocowanie obrabianych lub montowanych elementów. Składają się z trzech elementów: korpusu, właściwego docisku oraz mechanizmu mocującego. Urządzenia tego typu stosowane są podczas różnych procesów technologicznych. Ich funkcjonalność szczególnie ważna okazuje się w zakładach zajmujących się:
- spawaniem;
- klejeniem;
- montażem elementów i części maszyn przemysłowych (również w ramach linii produkcyjnych);
- obróbką mechaniczną przy użyciu maszyn takich jak tokarki, frezarki czy szlifierki.
Czemu warto stosować dociski szybkomocujące?
Szerokie rozpowszechnienie docisków to wynik wielu czynników. Jednym z najważniejszych jest fakt, że zapewniają wysoki stopień bezpieczeństwa i pełną precyzję w trakcie wspomnianych procesów. Użycie docisku eliminuje ryzyko przesunięć czy niekontrolowanych ruchów podczas prac, podnosząc tym samym efektywność i skuteczność poszczególnych operacji.
Obsługa docisków szybkomocujących jest prosta i intuicyjna obsługa. Dzięki temu poradzą sobie z nią nawet mniej doświadczeni operatorzy. Solidna konstrukcja oraz zastosowanie wysokiej jakości materiałów gwarantują zaś niezawodność i wytrzymałość nawet w warunkach przemysłowych. Nie sposób pominąć też różnorodności docisków. Na rynku dostępne są ręczne dociski szybkomocujące pionowe i poziome, modele pneumatyczne o zróżnicowanej budowie oraz prasy. Bez problemu można więc dopasować urządzenie dostosowane do konkretnego rodzaju prac.
Dobór docisków szybkomocujących. Na co zwrócić uwagę?
Komfort i bezpieczeństwo użytkowania docisku szybkomocującego w dużej mierze uzależnione są od doboru modelu odpowiednio dostosowanego do specyfiki danego zastosowania. By uniknąć ewentualnych błędów, należy zapoznać się z charakterystyką poszczególnych typów docisków. Najważniejsze z nich to:
- dociski ręczne poziome: przeznaczone do mocowania elementów w pozycji horyzontalnej i stosowane przede wszystkim przy operacjach na płaskich elementach – np. frezowaniu, szlifowaniu lub wierceniu;
- dociski ręczne pionowe: przystosowane do prac wymagających jak najlepszego dostępu do dociskanych elementów – np. w obróbce CNC;
- prasy dociskowe: umożliwiają pracę z elementami o dużej wadze – np. obróbkę drewna i płyt meblowych lub spawanie metali;
- dociski pneumatyczne: sterowane sprężonym powietrzem, oferują duży kąt rozwarcia i możliwość regulacji siły, co jest istotne przy częstym otwieraniu i zamykaniu docisków. Umożliwiają niezależną pracę kilku docisków w jednym momencie oraz sterowanie nimi z różnych miejsc.
Dociski szybkomocujące – precyzyjna i bezpieczna praca
Inwestycja w odpowiednio dobrane, wysokiej jakości dociski szybkomocujące to nie tylko krok w kierunku optymalizacji procesów produkcyjnych, ale też pewność co do bezpieczeństwa operatorów i zwiększenie efektywności prac. Znajomość różnych typów docisków oraz ich właściwości pozwoli inwestorowi dopasować narzędzie do konkretnych potrzeb – decyzję o wyborze danego modelu należy więc dokładnie przeanalizować.
Ich zastosowanie obejmuje unieruchomienie obrabianych lub montowanych elementów w zakładach rzemieślniczych i przemysłowych.
Użycie docisku szybkomocującego zapobiega poruszaniu elementów, co korzystnie wpływa na precyzję, wydajność i bezpieczeństwo całego procesu.
Najważniejszym czynnikiem przy wyborze docisków jest ich rodzaj. Modele poziome, pionowe, pneumatyczne i prasy dociskowe mają inne zastosowania i sprawdzają się w pracy z innymi elementami.